Let's take a tour: Behind the scenes at Bailey of Bristol
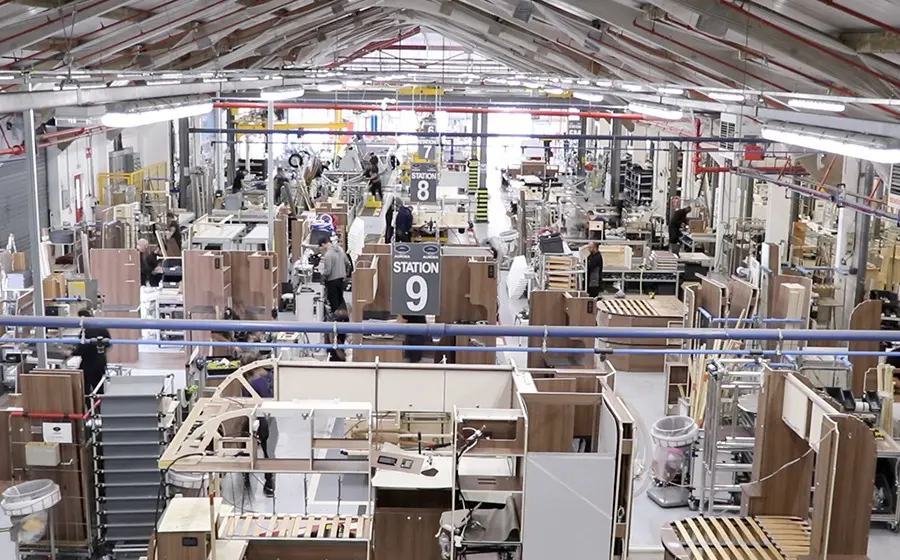
After some negotiation I was also allowed to film the process of construction from raw components to a complete caravan ready for dispatch.
The build process starts on the outskirts of the city and just off the M5, where the panels are created. The Bailey Large Panel plant creates all the panels, roofs and floors for the entire range of caravans and motorhomes in the Bailey line up.
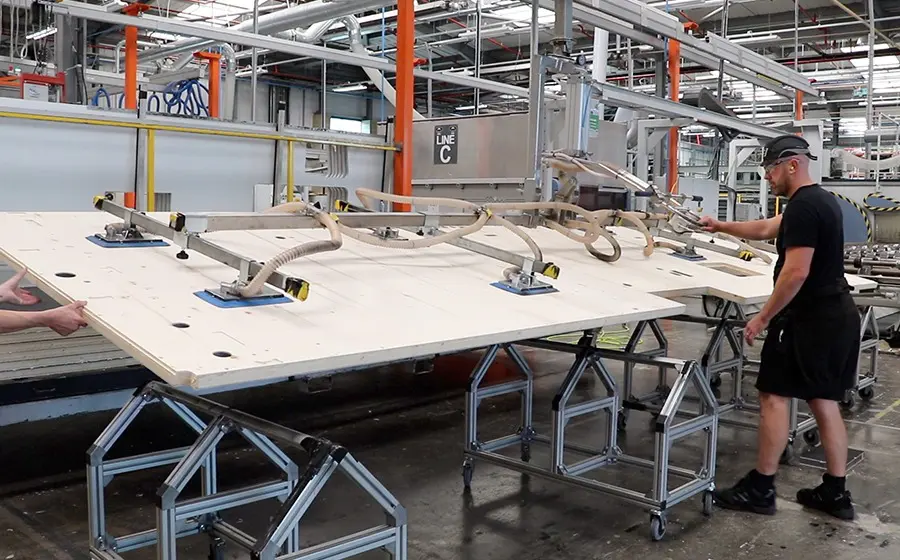
The facility is split into 4 separate lines. 2 lines create the left and right sides, one line creates the roof panels (which also include the rear) and finally the last line creates the floors.
The production is timed to line up with the main construction of the caravans back at Bailey HQ where regular shipments of the panels, floors and roofs take place throughout the day.
Here is part 1 of my video where I witness the construction method used to create the Alu-Tech panels and learn what really goes into building a caravan.
Once all the panels have been built and shipped to Bailey HQ, the construction of the caravan can take place. The production line starts with the floors that we saw at the end of the video in part 1. The floors are equipped with the wheel boxes, vents and are fitted with the main vehicle electrics. Meanwhile an AL-KO chassis is built alongside and bolted in place along with the axle and hitch. Once secured in place, the entire assembly is flipped and sent on its way to have all the furniture added.
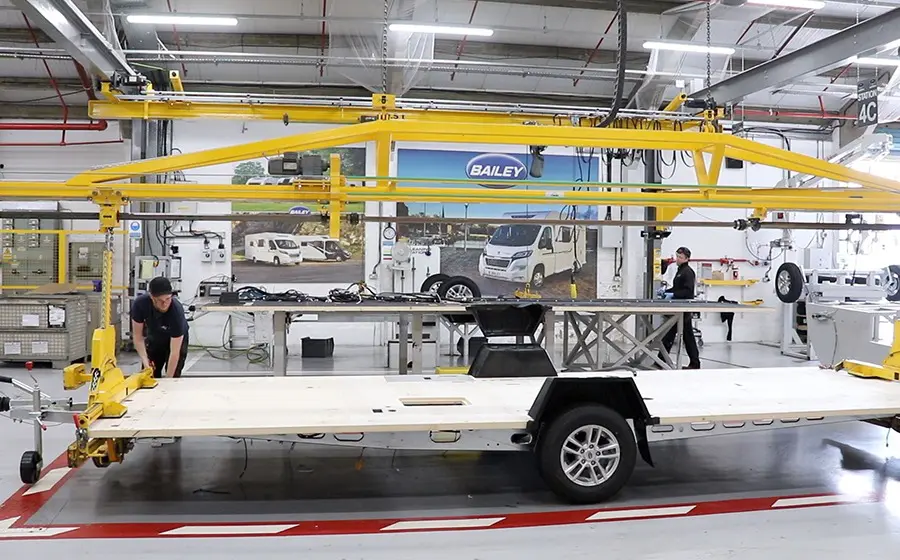
I was surprised to see the inside of the caravan being created before the panels were added. Large items are added in first, then overhead lockers and finally the sides, back and roof are secured in place.
I was also impressed to see just how the Alu-Tech system works. The panels are aligned and bolted together in a uniform and constant method. All the bolts are tightened with specific torque settings, which means the caravan is not solely reliant on glues or adhesives that make the final construction.
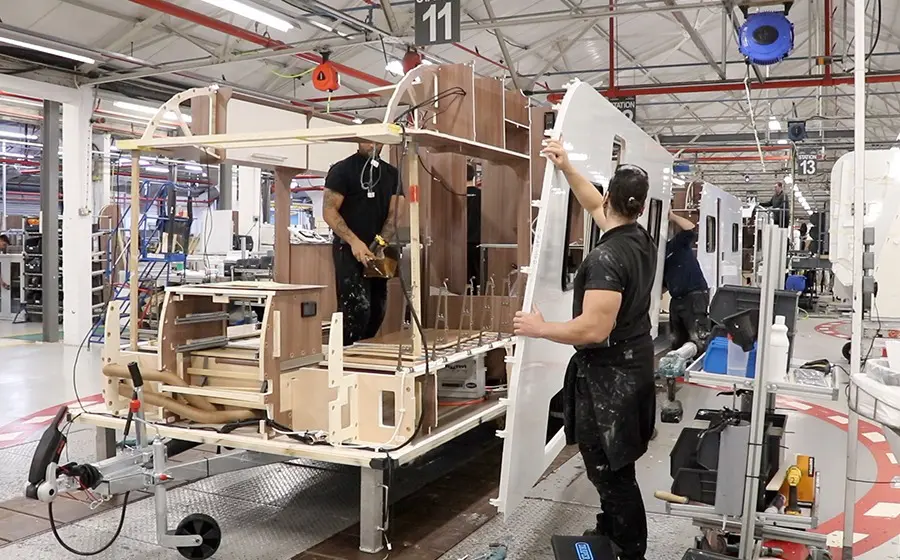
Here is Part 2 of my tour of the Bailey factory. This part watches all the components come together and a finished caravan is rolled off the production line.
It was a mighty impressive tour of the Bailey factory floor. I saw some amazing things and I was also impressed with the engineering of how all the components fitted together.
Seeing the bare caravan without the sides gave me a real appreciation of how much work and effort goes into a modern Bailey caravan. I would like to thank Bailey of Bristol for allowing me to tour both facilities and apologies for getting in the way of the teams of people who were doing their day job.
Next
News & Events